Trenchless pressure pipe rehabilitation with swagelining
The requirement was the trenchless functional testing and rehabilitation of a 600 m long free-fall pressure pipeline (DN 700, cast iron) dating from 1928. An optical inspection was performed and measurements were made in preparation for this.
Challenge
Rehabilitation of a pressure pipeline of decisive importance and the only discharge possibility to the main pumping station of Cracauer Anger by the sewer specialists of Frisch & Faust Tiefbau GmbH on behalf of Abwassergesellschaft Magdeburg mbH for the East Elbe drainage area of Brückfeld, Cracau and Prester. The pipeline route crosses a residential area between one of Magdeburg's largest pumping stations and a pressure relief shaft in the vicinity of a busy road intersection. In addition, there is an old tree population in the immediate vicinity of the pressure line. Accordingly, traffic and environmental concerns were to be taken into account in the project and obstructions for residents were to be reduced as far as possible.
Solution
Condition assessment by camera inspection
For the planning and execution of a suitable process, Frisch & Faust carried out a careful damage analysis of the old pipe. This was preceded by the installation of a transfer line through which the wastewater was diverted.
Profile dimensioning
To ensure the greatest possible reliability in the execution of the intended rehabilitation, the real profile dimension was determined over the entire run of the pressure pipe. For this purpose, a continuous, laser-supported profile dimension measurement was carried out with the IBAK ORPHEUS 2 pan and rotate camera. The results of the measurement served Frisch & Faust as a basis for rehabilitation planning.
The lasers integrated in the fully rotatable camera head were used to determine the profile dimensions over the entire length of the pipeline. The IBAK T 86 camera tractor travelled at a constant speed of about 5 to 7 cm/sec. The laser points recorded in this way were analyzed with the IKAS evolution software and evaluated by Frisch & Faust.
Pipe run measurement
In theory, the location of main sewers can be determined from manholes. It is generally assumed that the sewers run in a straight line between the manholes. The pressure pipe to be rehabilitated does not run in a straight line between the inspection openings. The bend deviation was not precisely known and was so significant that it was of importance for the planning of the rehabilitation measure. Based on these considerations, the exact run of the pressure pipe was recorded with x,y,z coordinates in the present case. For this purpose, IBAK 3D GeoSense pipe run measurement was used. The 3D sensor integrated in the IBAK ORPHEUS 2 pan and rotate camera was used to record the run of the pipeline during the camera inspection.
Result
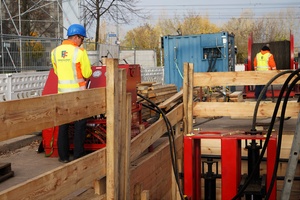
Detection of incrustations and spongiosis as defects in the old pipe by optical inspection. This showed that the old pipe was under a potentially higher risk of fracture and lacked mechanical load-bearing capacity. On this basis, it was possible to select a suitable and economical method of rehabilitation and an accurately dimensioned PE pipe with an optimal fit.
The laser scan of the pressure pipe made it possible to obtain data and thus gain insight that goes beyond that of a purely optical inspection. Analysis of the measurement revealed, among other things, a minimum measured diameter of 692 mm. As the maximum and minimum diameter over the entire length of the pressure pipe was known, a PE pipe could be selected to match.
The 3D-GeoSense pipe run measurement immediately provided a realistic site plan with width, length and height data. The geodetically accurate site measurement completed the information about the sewer to be rehabilitated and was taken into account when the rehabilitation procedure was decided upon. The generated site plan was the basis for deciding into how many sections the installation work had to be divided.
Company introduction
Frisch & Faust Tiefbau GmbH was founded in 1991. Since September 2007, the company has been under the management of shareholder and managing director Thomas Frisch and has generated an annual turnover of over 16 million euros.
Approximately 160 employees and trainees have successfully completed several thousand civil engineering projects throughout Germany in recent years. Controlled pipe jacking, open sewer construction, sewer rehabilitation and pipeline construction are the main focus of the supplier.